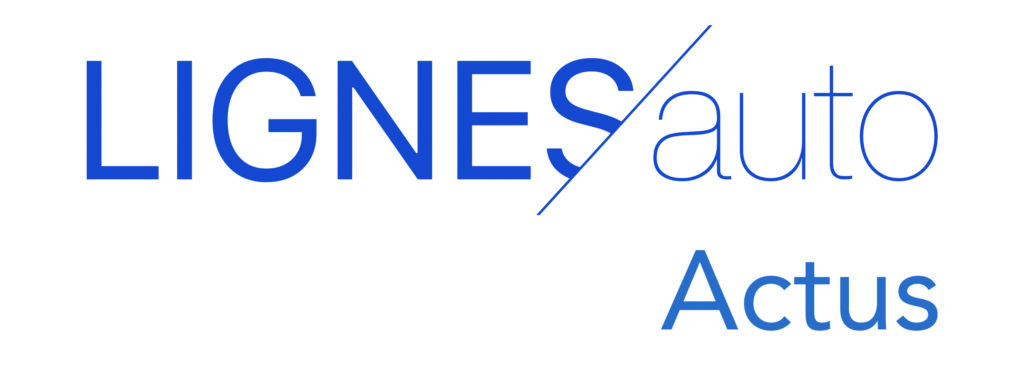
LIGNES/auto, c’est aussi une page Facebook : https://www.facebook.com/lignesauto/?modal=admin_todo_tour
Nous allons plonger dans l’univers d’un constructeur de l’hyper-luxe. Marque née française appartenant au groupe Allemand Volkswagen, Bugatti vient de célébrer la production du 200e exemplaire de la Chiron. Découvrons comment cette supercar est produite à Molsheim. (partie 2 sur 2)
Photos Bugatti communication, Benjamin A. Monn
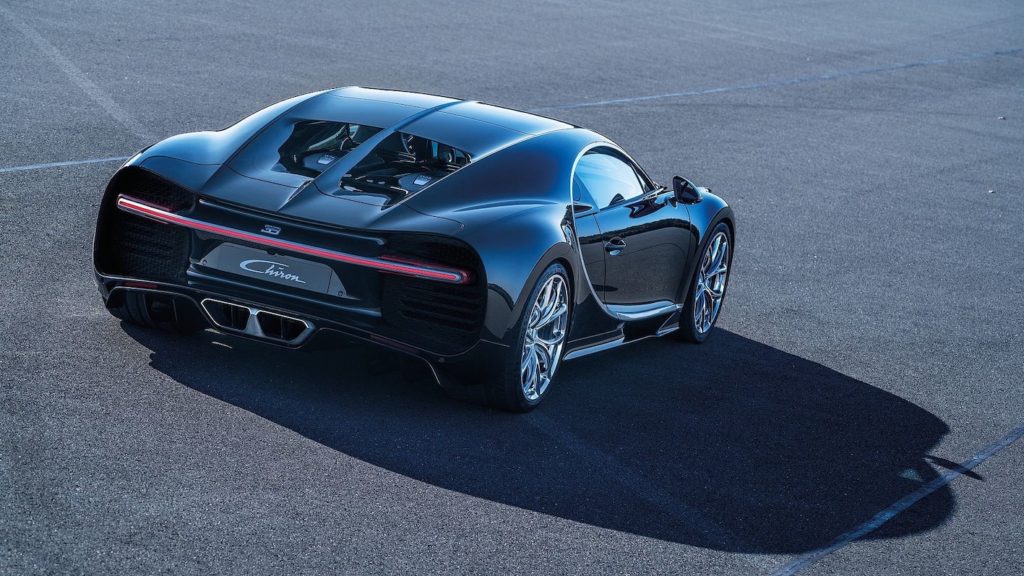
(Suite de la partie 1)… La deuxième zone de production est destinée à l’assemblage du châssis et du groupe motopropulseur de 628 kg, qui, grâce à l’utilisation accrue de carbone et d’autres matériaux légers, ne prend pas un gramme de plus que celui de la Veyron, malgré ses 300 chevaux supplémentaires.
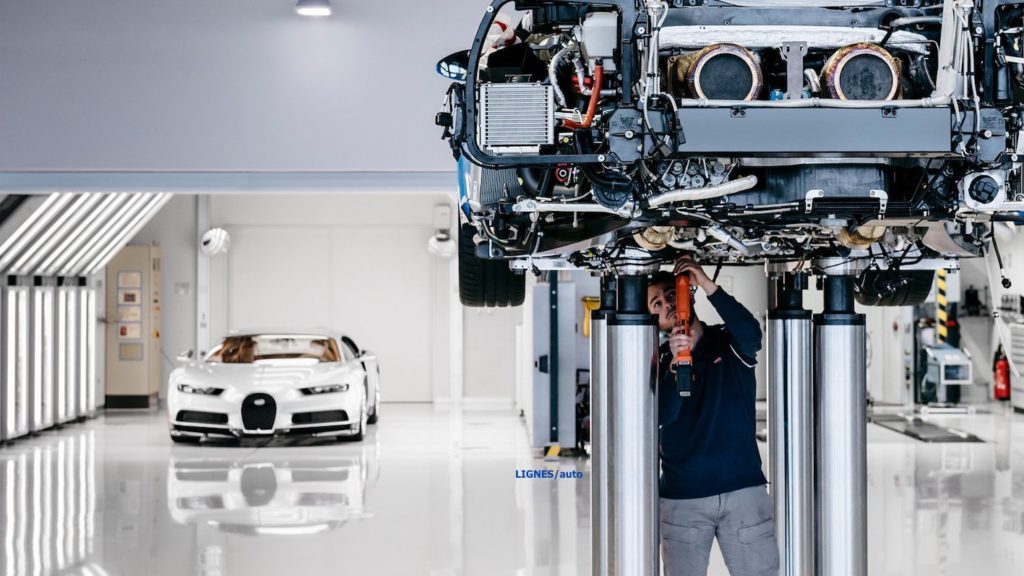
L’atelier comprend deux postes de montage pour le châssis, sur chacun desquels travaillent trois collaborateurs. Une semaine leur est nécessaire pour l’assemblage et, contrairement à un ouvrier à la chaine classique, il leur faut maîtriser le montage complet du châssis, c’est-à-dire la partie arrière, la monocoque et la partie avant qui constitue l’élément de structure.
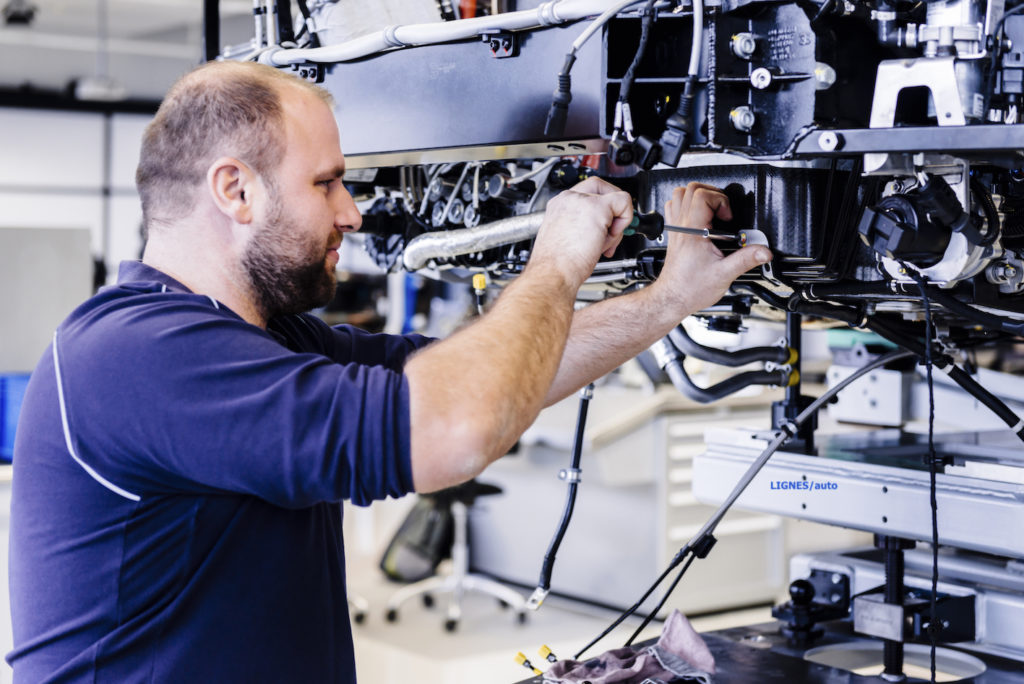
Pendant que le montage de la partie arrière, articulé autour du groupe motopropulseur, est effectué, la monocoque et la partie avant sont assemblées entre elles, puis complétées par les câblages nécessaires et les tubulures reliant le moteur à l’arrière aux radiateurs à l’avant. Le système de refroidissement est équipé de trois pompes de liquide de refroidissement. Le diamètre des tubulures correspond à celui d’un tuyau d’incendie, ce qui assure une capacité de débit élevée.
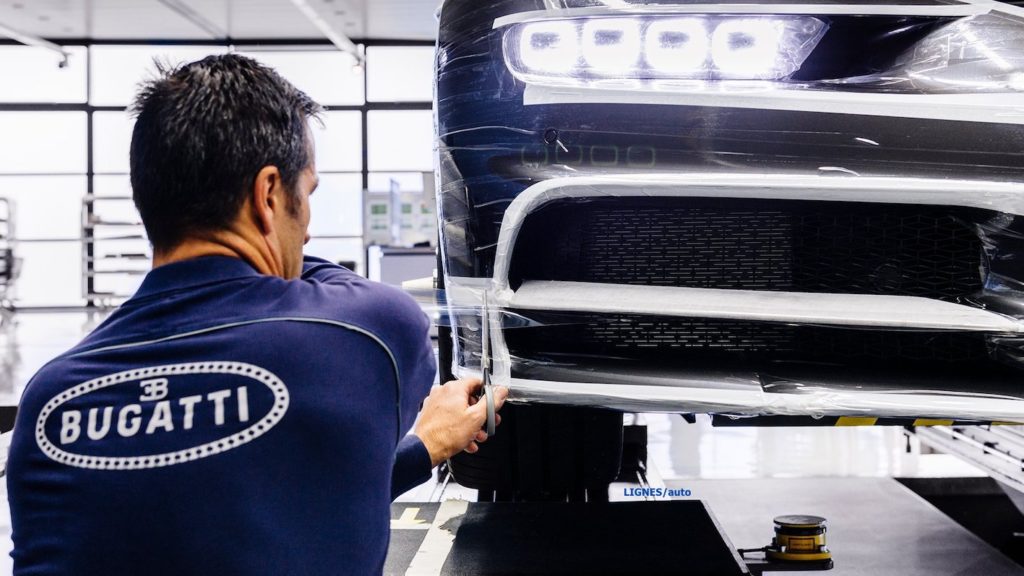
Les seules assistances électroniques utilisées lors du montage du châssis sont les nouvelles stations de vissage. Elles permettent de mémoriser chaque vissage dans un ordinateur qui signale au monteur lorsque le serrage a atteint le couple adéquat. Il y a plus de 1800 points de vissage sur une Chiron, dont 1068 sont documentés dans le système. Le point d’orgue du montage du châssis est sans aucun doute le mariage de la monocoque et de la partie arrière. Quatorze vis en titane garantissent la liaison extrêmement résistante des deux éléments.
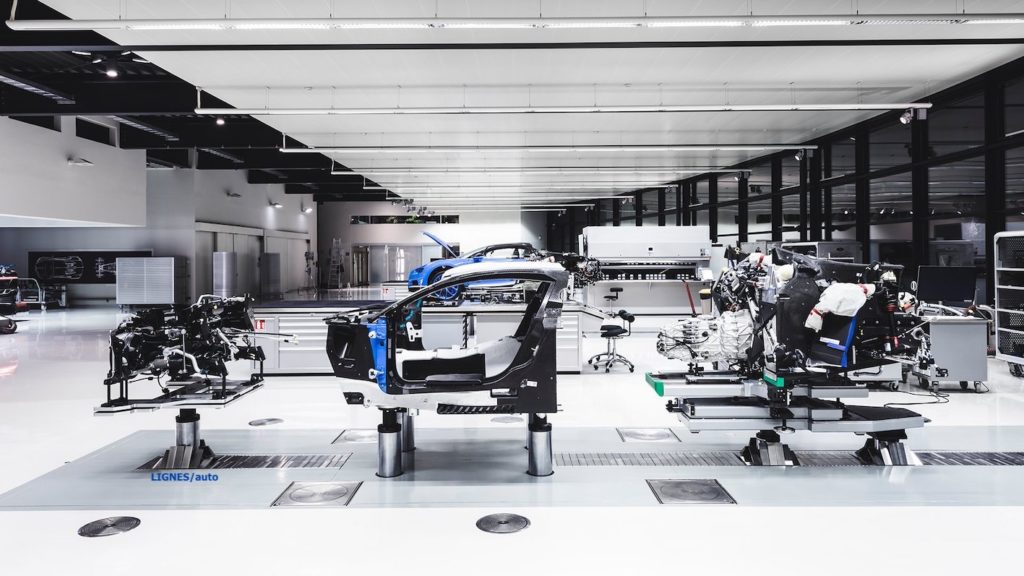
La dernière étape du montage du châssis voit celui-ci recevoir ses 4 roues avant de rouler vers la zone de production suivante : la station de remplissage. Elle sert à apporter tous les liquides dont le véhicule a besoin : l’huile moteur, l’huile de transmission, le liquide de frein, le fluide hydraulique et le liquide de refroidissement qui est aspiré sous vide et soumis à un test d’étanchéité du circuit pendant 10 minutes. Ce poste est également celui ou le moteur 16 cylindres est mis en marche pour la première fois, moment toujours particulier pour les collaborateurs.
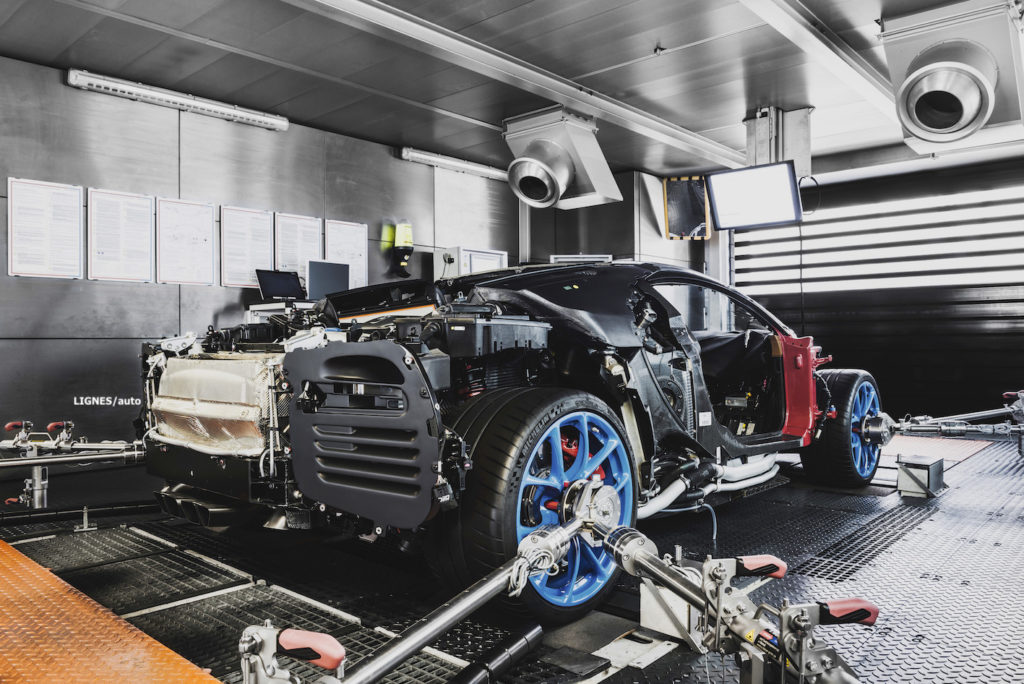
Le châssis est ensuite amené quelques mètres plus loin au banc dynamométrique, qui représente le plus gros investissement réalisé dans le cadre de la transition de la production de la Veyron à la Chiron. La nouvelle installation est désormais si puissante qu’elle peut produire une énergie électrique allant jusqu’à 1 200 ampères. Cette énergie excédentaire est alors redirigée vers le réseau électrique de la commune de Molsheim. Le banc dynamométrique de Bugatti est le plus puissant au monde dans sa catégorie. Ce banc d’essais permet de simuler des vitesses s’élevant jusqu’à 200 km/h ainsi que des accélérations à plein régime (1 500 chevaux).
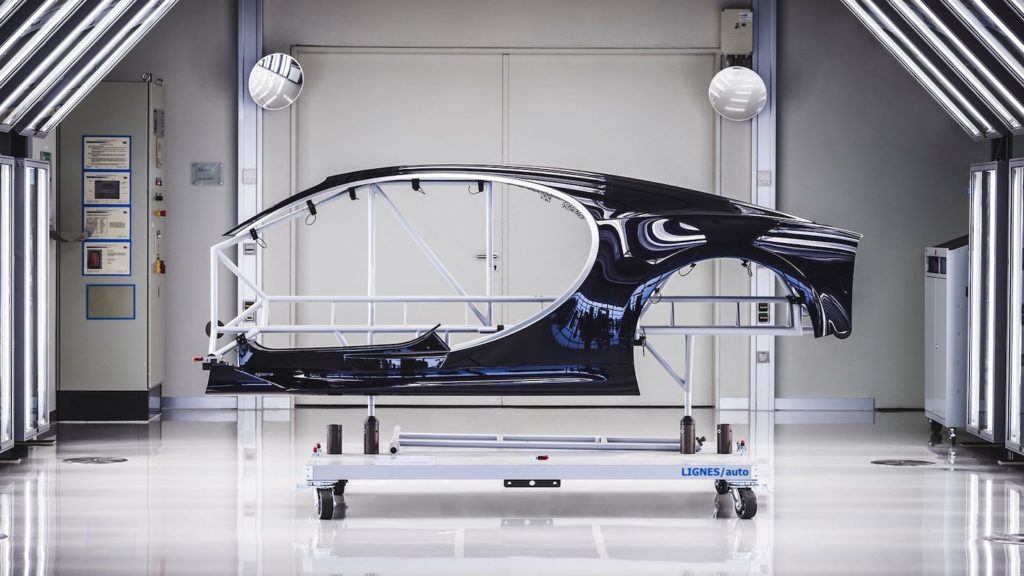
Si la Chiron valide tous les tests, elle peut passer à la zone de production suivante et recevoir sa carrosserie dont tous les éléments sont entièrement constitués de carbone. Étant donné que certains composants légers sont volumineux et fragiles, ce qui rend cette étape particulièrement délicate, une étape de prémontage a été mise en place.
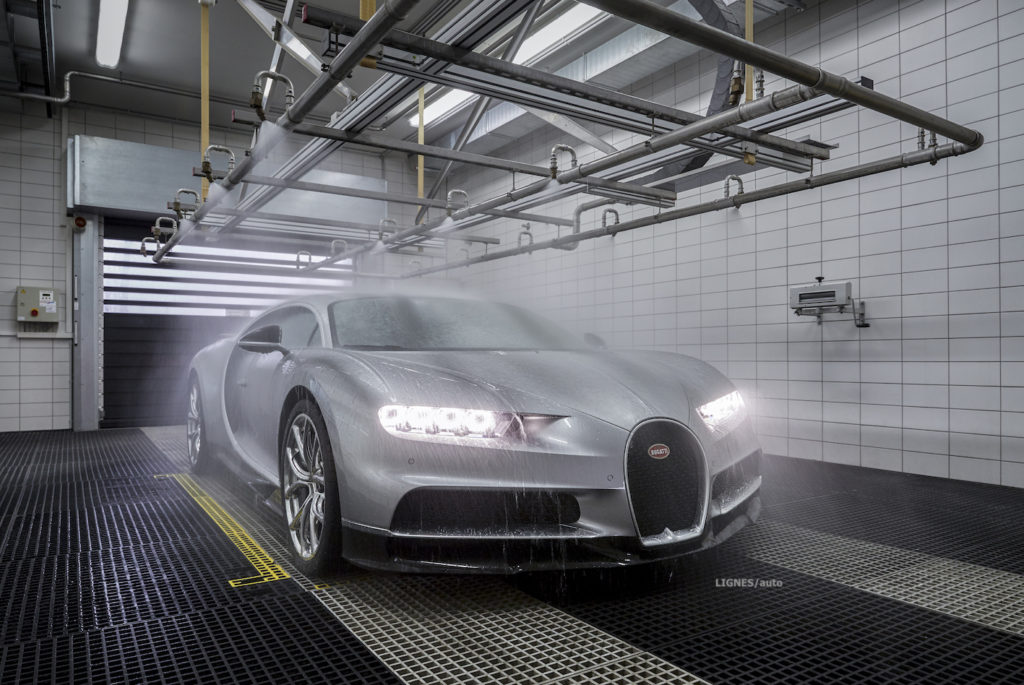
Prochaine phase : le test d’étanchéité. La Chiron « prend une douche » d’une demi-heure comparable à une pluie de mousson avec des intensités variables. Ce n’est qu’une fois ce test réussi que la pose de l’intérieur peut débuter. Durant cette étape, qui dure en général environ trois jours avec deux collaborateurs. La Chiron est ensuite préparée pour les essais sur route et de réception. Elle est pour cela d’abord entièrement recouverte d’un film résistant aux gravillons et transparent. Ce processus seul dure une journée complète, la même durée est nécessaire à la dépose du film et au nettoyage du véhicule après les essais. Pour l’essai sur route, Bugatti n’utilise pas les roues du client ni le soubassement du véhicule final, de manière à les préserver. Durant l’essai de réception, la Chiron parcourt 300 km à travers les Vosges jusqu’à l’aéroport de Colmar afin d’utiliser sa piste d’atterrissage. Elle y est soumise à un test fonctionnel pour lequel il est nécessaire d’ accélérer au-delà de 250 km/h. Le retour vers Molsheim se fait alors plus « confortablement » sur l’autoroute pour refroidir le véhicule.
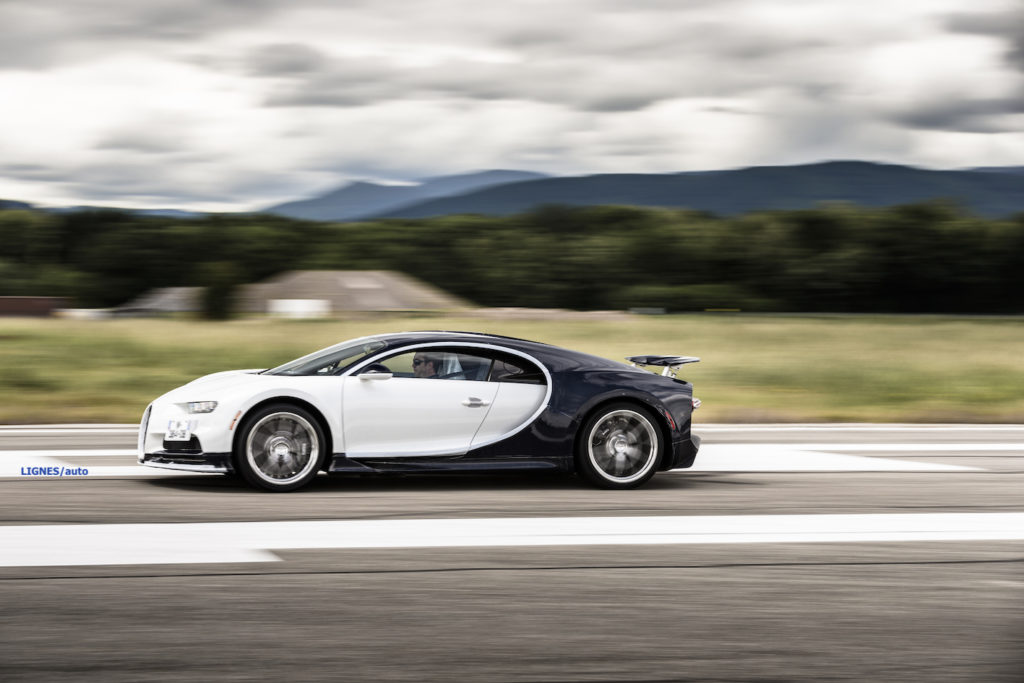
La Chiron passe ensuite par la cabine de peinture, où on lui retire les films de protection avant de la nettoyer et de la polir. Ce soin de beauté dure en général deux jours, puis le véhicule est amené dans le tunnel lumineux, dans lequel un collaborateur l’inspecte pendant plus de six heures sous toutes ses coutures, d’un œil affûté et impitoyable. S’il repère des défauts, il renvoie alors la Chiron dans la cabine de peinture où son collègue se consacrera à les éliminer. Cela peut durer entre trois heures et trois semaines, dans le cas où une pièce unique doit de nouveau être produite.
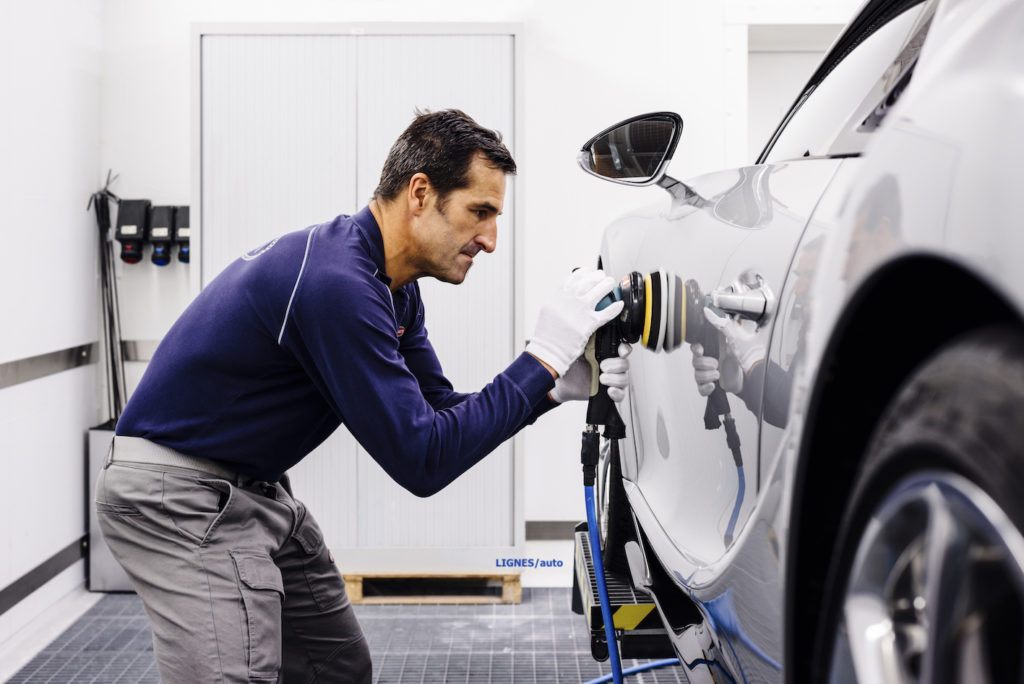
Lorsque l’auditeur du tunnel lumineux valide finalement l’extérieur du véhicule, Christophe Piochon se réunit alors avec les responsables des départements Vente, Assurance qualité et Service client pour la validation finale. Une fois que tous sont satisfaits du résultat, un rendez-vous peut être convenu avec le client pour la remise de la Chiron. Avant cela, celui-ci se sera déjà néanmoins rendu plusieurs fois à Molsheim. Ainsi, outre pour l’essai sur route dans un véhicule de démonstration, la signature du contrat de vente et la configuration de leur future Chiron, les clients se rendent volontiers à l’atelier pour suivre en personne l’avancement du processus. Ils ont même la possibilité de participer durant une journée à l ́assemblage de « leur propre » voiture de sport.
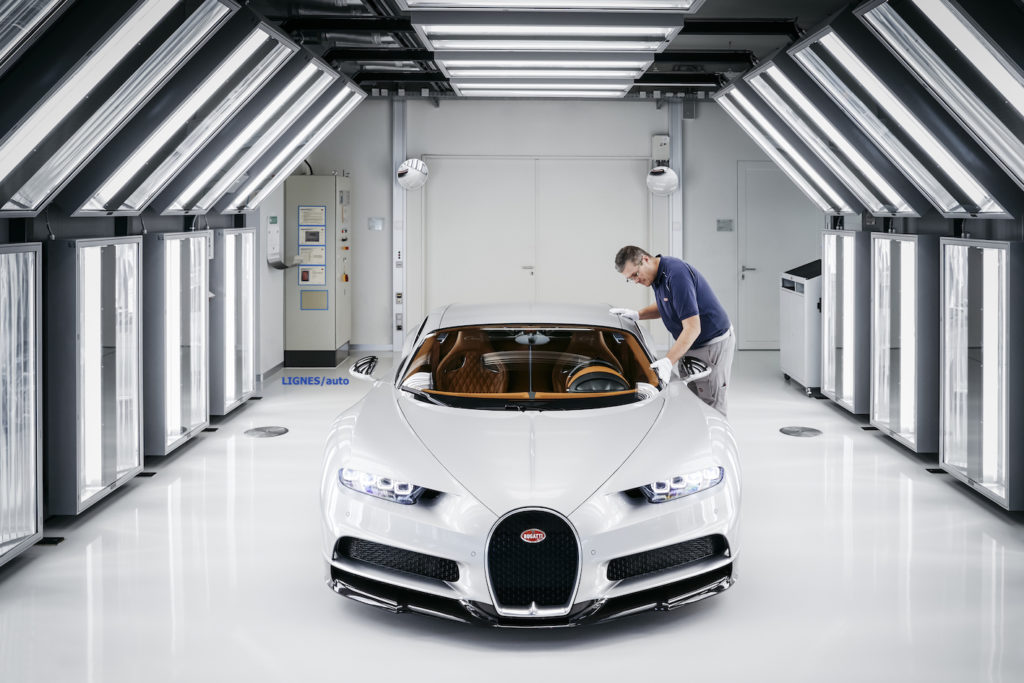
Après environ deux mois, la Chiron peut enfin quitter l’atelier. Pendant cette période, vingt collaborateurs, dont deux femmes, ont assemblé environ 1 800 pièces, dont le tout forme la supercar de série la plus puissante, la plus rapide, la plus luxueuse et la plus exclusive au monde. Ils sont épaulés par 17 collaborateurs qui s’occupent de la partie logistique ainsi que par 15 autres chargés de l’assurance qualité.
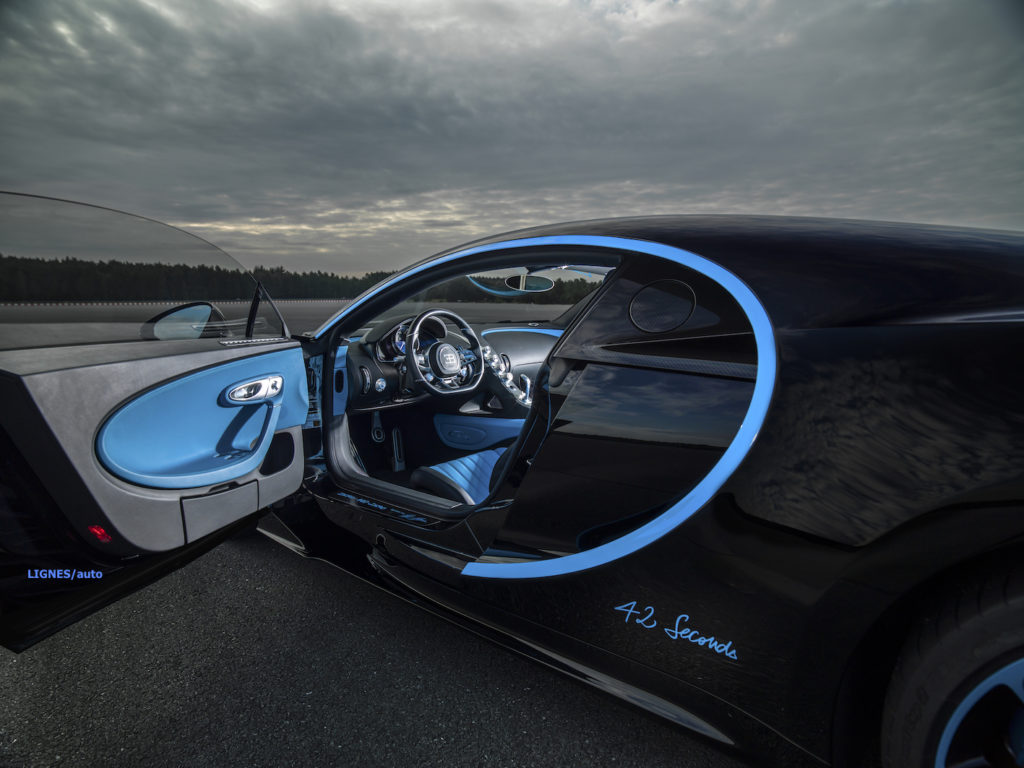
“La qualité et la main d’œuvre forment les deux branches de l’ADN de Bugatti. Tout comme il y a 110 ans, nous faisons très attention à la sélection des matériaux et à leur qualité.” explique Stephan Winkelmann, Président de Bugatti. “Le fondateur de l’entreprise Ettore Bugatti disait qu’un produit technique n’était parfait que lorsque qu’il est parfait d’un point de vue esthétique. Cela inclut la main-d’œuvre.” C’est pour cela que le contrôle de la qualité a une grande signification.
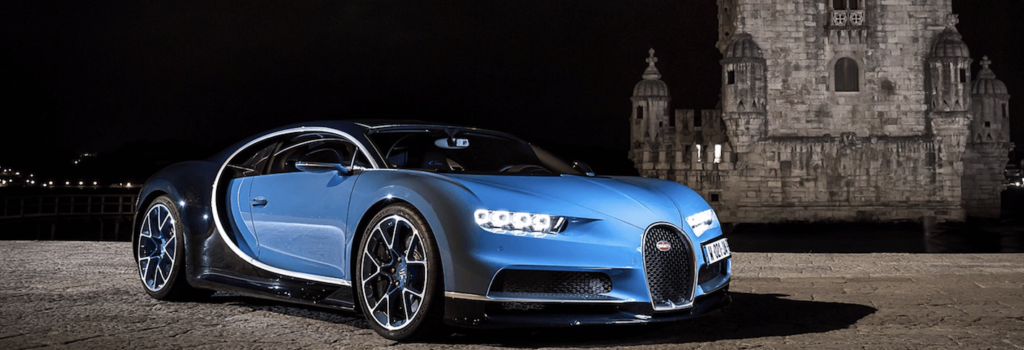
En 2018, Bugatti a produit 76 Chiron. Cette année, ce sera plus de 80 véhicules, avec les premières Bugatti Divo (ci-dessous). En conséquence, la manufacture française continue d’investir pour le futur et engage 20 nouveaux employés dans les départements de production et de logistique.
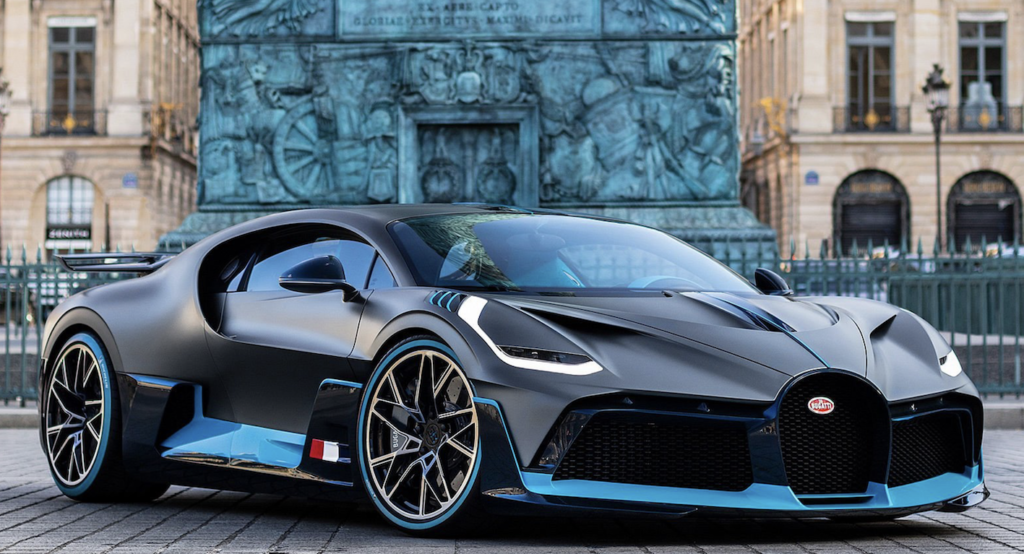
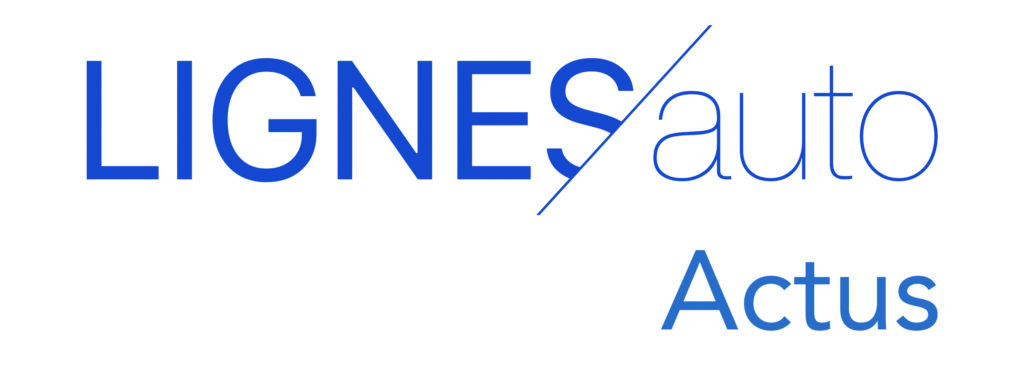